Case Study:
Foam Seat
Manufacturer
1 Introduction
2 Tracking: Production Line
3 Tracking: Supply Chain
4 System Architecture
5 Goals Achieved
Introduction
This case study describes the RFID project for a foam car seat manufacturer based in the North of
England. The manufacturer faced a problem in tracking their product through the production line as
well as along the supply chain. We developed and set up an RFID system that tagged and tracked the
product, allowing the manufacturer to know:
1. When the product was created
2. When the product passed specific points along the production line,
3. When it was shipped out to the customer and
4. When the customer received it at their Goods In.
Objectives
The company's objectives were:
1. To have real time tracking of individual items along the production line
2. To have live snapshot information of the status of all items in production
3. To have historical information of all items that have been manufactured, and the specific toolset
that was used in the manufacture of each individual item
4. To implement checks and controls during the movement of goods along the supply chain
Tracking along the Production Line
RFID tags in the product helps to
track the item along the various
stages of the Production Line
The company creates foam seats using specific moulds for specific seat types and these are added
to a production line which circles round from a start point to an end point. The moulds are filled at
the start point in the production line and the completed foam seats are removed after successful
processing.
We produced software that manages the encoding and verification of production line tags. An
embedded tag, termed an Inset Tag, is embedded into the foam seats at the start point of the
manufacture. Information about each specific tool used is written onto the embedded tag every time
the tag passes a tool. This allows the traceability of which tool was used at each stage of production
to produce the product. The tool tag data also includes a timestamp which allows for auditing and
tracking of the Inset Tag.
Tracking along the Supply Chain
GoodsOut at Manufacturer's Site
The company also wished to track their products as they moved out from their warehouse, and
throughout the journey as they were bring received in the Goods In of their customer's site. The
objective here was to ensure that no goods were lost in transit, and to ensure that any seats that did
not meet customer satisfaction could be traced to a specific production line and tool set.
This was implemented using an RFID fixed portal scanning system which
facilitated the tracking of production items moving from the production area
out to the warehouse. The foam seats were packed in plastic crates/boxes,
with a single box to contain between 40 and 42 seats. As each seat had one
tag, if less than 40 or more than 42 tags were read, this would be flagged as an
error and trigger a visual alarm (red light) and a warning noise via a sounder.
The RFID tags also included information about the product group, and all the
items in a crate had to have the same product code. In the event this was not
true the visual alarm would be triggered. If no errors were encountered a green
light would flash silently.
GoodsOut at Manufacturer's Site
An RFID fixed portal scanning system was also installed at Goods In at the Customer's site. This
allowed for the crates that were sent to the customer to be scanned on receipt, and any loss during
transit to be recorded at the point at which the crates are received by the customer.
As the seats were unpacked and picked up for further processing, any seat that did not meet the
customer satisfaction could be marked as such. The tag would be read and the details of the entire life
of that individual seat from the point of creation, to the list of each and every tool that was used in the
production of that seat would be displayed. This allowed for quicker identification of problems such as
deteriorating moulds along the production line.
System Architecture
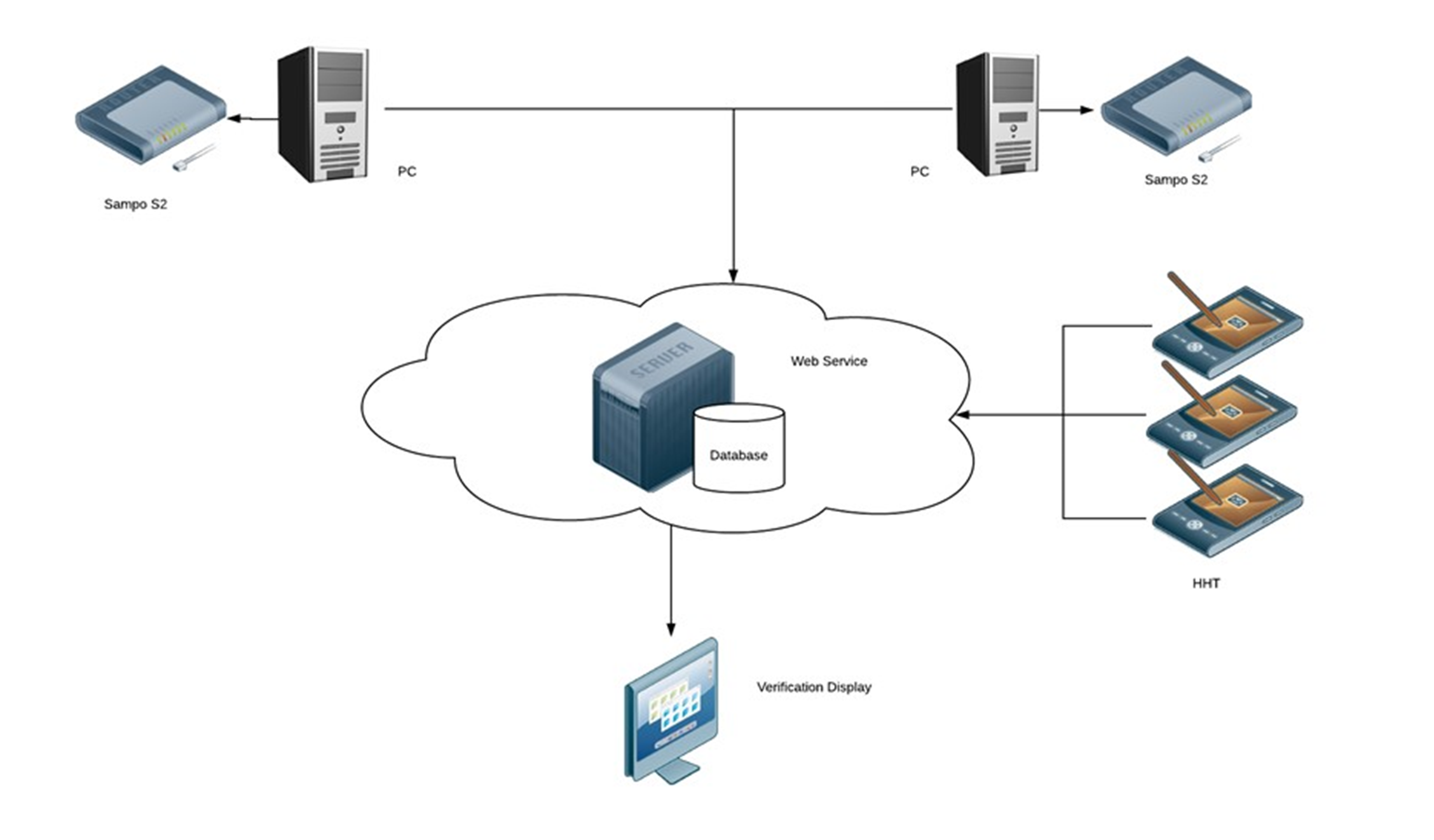
Technology Stack
The system depicted above provides a logical view of the various components. In the case of
using USB connected Sampo Readers, each reader will need to be connected directly to a single
PC. One PC will form the Encoding Station to encode the tags and have the appropriate software
for this purpose and the second PC will be set up as the Verification station.
In addition both the Verification and Encoding software application make use of a Web Service
which is in turn attached to a single SQL Database. This Web Service provides a simple RESTful
API to enable the two stations to record and retrieve the tag information.
This Web Service can be hosted on a third, separate PC or on a cloud.
Goal Achieved
100%
Journey of products tracked from creation to the point at which customer satisfaction was recorded
The RFID tracking system:
• Provided the manufacturer with real time information about the production.
This helped them to take proactive steps as necessary to achieve the Just In
Time manufacturing goals.
• Allowed them to identify tool sets that were wearing out, and goods lost or
damaged during shipment to their customer site.
Key challenges overcome:
• Ensuring the accuracy of RFID tags being read, without reading adjacent tags
in error
• Accurately identifying and mapping the process flow in case of error
conditions